Always-on product availability with faster, smarter global supply chain
Overview
Semiconductor manufacturers operate in one of the most demanding supply chain environments, balancing precision, speed and flexibility. For a leading global provider of semiconductor assembly and test services, fragmented systems and manual processes were slowing down operations across facilities in Singapore, Thailand, Indonesia and China. The lack of unified data and reactive inventory practices restricted their ability to meet fast-changing customer demands.
Partnering with us, the company embarked on a complete transformation of its supply planning operations. Leveraging Blue Yonder Enterprise Supply Planning (ESP) and custom-built integration frameworks, we introduced AI-powered inventory optimization that reshaped their entire planning process. This resulted to a more responsive, data-driven supply chain with significantly reduced costs and enhanced agility.
The Challenge
Semiconductor supply chains demand precise coordination across global operations with accurate, timely data processing. The manufacturer's existing infrastructure presented significant operational barriers:
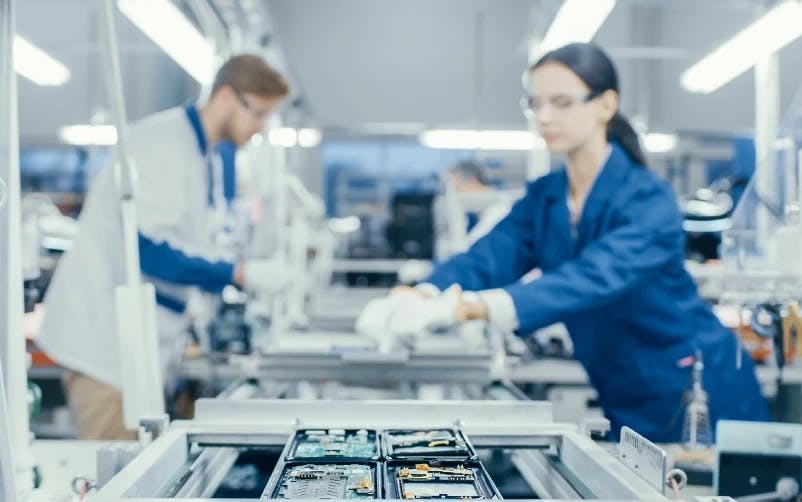
- Fragmented data environment: Multiple disconnected systems created an integration bottleneck
- Manual data handling: Massive data volumes required extensive manual handling, leading to delays and accuracy issues
- Limited inventory visibility: Fragmented systems prevented comprehensive oversight of global inventory positions
- Reactive supply model: The push-based distribution model limited responsiveness to demand fluctuations and market changes
The company needed a unified, intelligent supply planning solution that could process complex data at scale while enabling more agile inventory management across its global manufacturing footprint.
The Solution
Through a collaborative eight weeks of discovery workshops, we designed and implemented an intelligent, AI-powered supply planning transformation, our approach delivered:
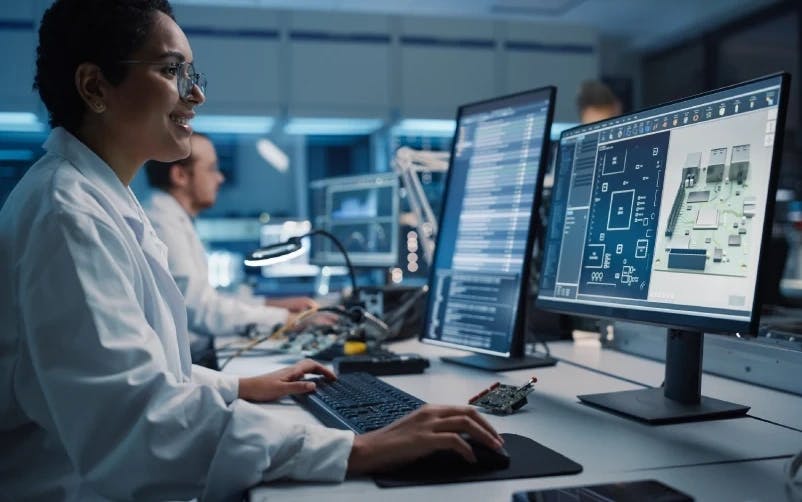
- Intelligent demand classification framework: Machine learning algorithms categorized products based on demand patterns, enabling smarter inventory allocation
- Automated safety stock calculation: Data-driven models determined optimal safety stock levels across locations, balancing availability with cost
- Push-to-pull model transformation: The supply model shifted from forecast-driven to demand-driven distribution, enabling immediate response to demand spikes and changing customer preferences
- Advanced integration architecture: Custom APIs extracted data from diverse source systems, creating a unified data environment for planning decisions
- Comprehensive analytics dashboard: Development of specialized reports in Power BI, providing unprecedented visibility into supply chain performance
This integrated solution streamlined the entire planning process, from data collection to execution, while introducing AI at every decision point.
The Impact
The transformation delivered measurable results across the supply chain:
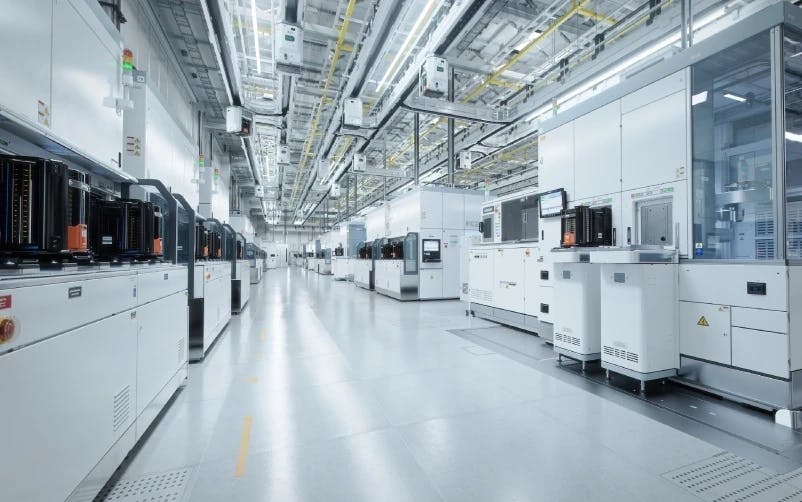
- 30% reduction in distribution expenses by optimizing inventory placement reducing transportation and handling costs
- 8% reduction in store inventory and 25-30% reduction at warehouses, releasing tied-up capital
- 10-12% reduction in safety stock levels while maintaining high service standards.
- 20% increase in supply chain productivity, empowering teams to focus on growth initiatives.
Beyond the Numbers
This transformation fundamentally changed how our client approaches supply planning. Moving from disconnected systems and reactive processes to an integrated, intelligent planning framework has created a more agile organization capable of responding swiftly to market changes.
The shift from a push to pull model marked a significant evolution in the company's distribution strategy, aligning inventory more closely with actual customer demand patterns. This change not only reduced costs but also improved customer satisfaction through better product availability and faster response times.
Supply chain teams now operate with significantly improved visibility into operations, spending less time gathering and reconciling data and more time making strategic decisions that drive business growth.
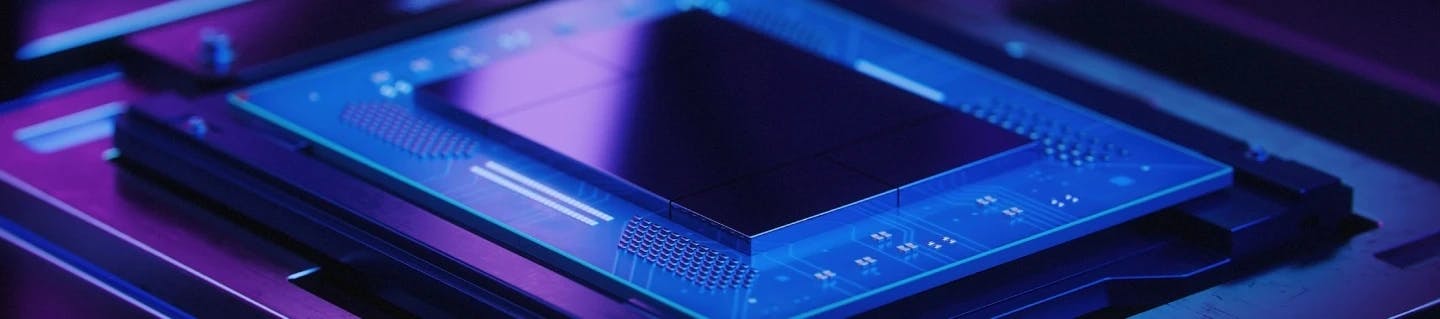
Celebrating Success
As they continue to expand their global operations, our intelligent supply planning framework provides the foundation for scalable growth enabling the business to respond with agility to market opportunities while maintaining operational efficiency.
Our partnership with this semiconductor leader demonstrates how advanced integration and AI-powered planning can turn supply chain operational complexity into a sustainable competitive advantage.