On time beverages, powered by predictive planning
Amid the disruption caused by the COVID-19 pandemic, a US-based brewing systems company partnered with HCLTech to strengthen its supply chain logistics. The goal was to harness advanced analytics to improve demand forecasting, boost fill rates and cut operational costs. Using Alteryx and Tableau, We implemented automated workflows and a modern analytics infrastructure that enabled the client to operate with greater speed, agility and accuracy across its nationwide distribution network.
The Challenge
The brewing systems company faced mounting supply chain challenges as consumer demand for beverages and appliances surged during the pandemic. Manual data evaluation processes and fragmented systems slowed response times and impaired forecasting accuracy. The influx of unstructured data from the legacy systems made it difficult to analyze consumption patterns and plan inventory effectively.
These issues exposed operational inefficiencies and underscored the need for an integrated, analytics-led approach to supply chain transformation.

The Solution
We delivered a comprehensive data and analytics solution focused on real-time visibility and predictive planning:
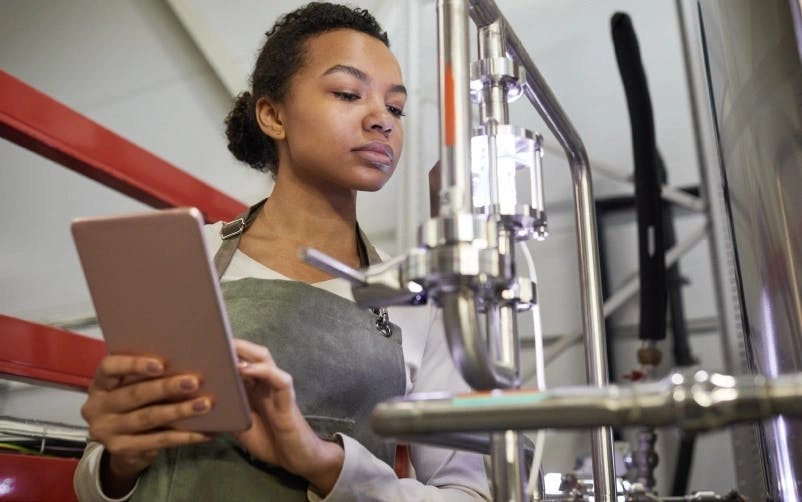
- Established three control towers to monitor supply chain performance and support agile decision-making
- Created over 30 custom workflows using Alteryx to help automatically gather, clean and organize data. This made it possible to predict customer demand up to four weeks ahead with better accuracy
- Developed advanced inventory alignment systems to optimize stock levels across warehouses
- Deployed a specialized team of four analysts, including experts in Alteryx and Tableau, to drive continuous optimization and logistics planning
The Impact
The analytics-led transformation significantly improved supply chain operations and cost efficiency
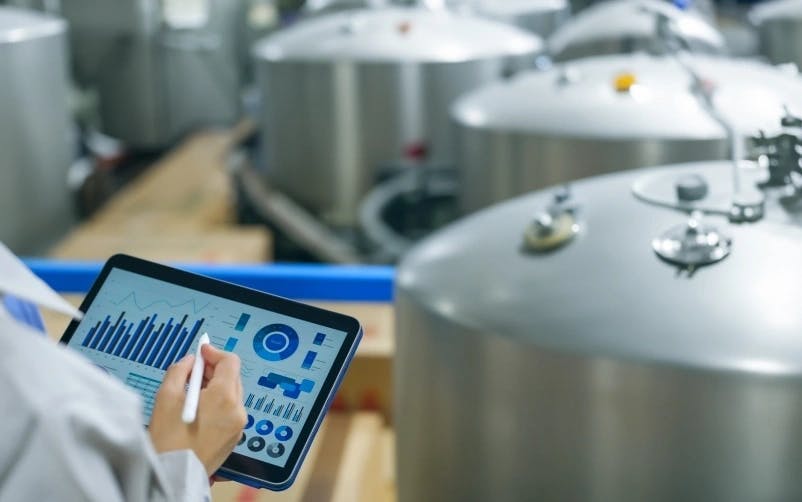
- The warehouse fill rate increased to 90%, with an average gain of 10 to 15% across the network
- The client saved $2M - $5M through improved demand forecasting and reduced overproduction
- Automated workflows and data refreshes reduced daily manual effort, saving analysts four hours each day and allowing more time for high-impact activities
Beyond the Numbers
With our support, the client transitioned from a reactive to a proactive supply chain model. The solution enhanced visibility across platforms, streamlined inventory management and accelerated decision-making through better forecasting.
The implementation of Alteryx Analytic Process and Automation (APA) Platform enabled a responsive logistics network capable of adapting to shifting demand. By reducing manual workloads, the engagement also improved employee productivity and enabled teams to focus on higher-value tasks.
Celebrating Success
Our collaboration with this brewing systems firm exemplifies how advanced analytics and automation can drive operational excellence and deliver Total Experience. By modernizing supply chain logistics, the company achieved improved forecasting accuracy, increased fill rates and significant cost reductions during the pandemic.
Our Blueprint to Total Experience report states that organizations that excel in delivering integrated experiences, also termed as 'Experience Leaders', realize an impressive 57% return on their Total Experience investments. This underscores the tangible benefits of a holistic approach that unifies customer, employee and user experiences.
As a trusted transformation partner, we continue to empower enterprises to harness the power of integrated experiences, driving resilience and growth in an ever-evolving business landscape.