Industry NeXT
HCLTech’s Industry NeXT framework extends the power of Industry 4.0 and enables global organizations to uncover transformational business potential by creating a cognitive ecosystem of connected experiences, resilient operations, and responsible business practices that power the next era of physical and digital products and services. It helps businesses realize their strategic goals and create differentiated value through the confluence of the next-gen workforce, integrated phygital assets, smart facilities, and sustainable operations powered by expansive digital interventions.
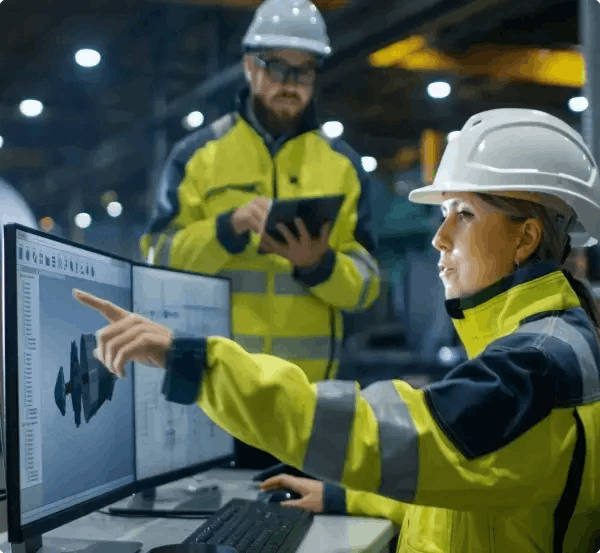
Offerings
Aligned with the critical needs of diverse industries, our Industry NeXT framework is structured around six pillars. Each pillar is supported by a team of technology and domain experts and powered by a comprehensive suite of pre-built solutions, frameworks, and deployable products. This approach enables businesses to effectively leverage digital technology and unearth untapped value.
Industry NeXT enables the future of value creation and value delivery is Expansive, to build on an increasingly connected and smart world. Adaptive, to cater for future business challenges and opportunities and Future-proof, to embrace new technology opportunities as they arrive
Cognitive Supply Chain
Realtime visibility and optimization of supply chain ecosystems by transforming the linear communications into connected ecosystems
Digital Manufacturing
Manufacturing value chain digitalization, data driven decision and actionable insight generation by leveraging AI/ML and Gen AI.
OT/IT Convergence
Seamless integration of OT/IT assets, devices or applications across the enterprise through omni-integration and communication platform
Product and Product Platforms
Connected and smart products for better customer experience, product value chain integration and new revenue generation models
Immersive and Remote technology adoption
Industrial metaverse for remote operations, visualization and assistance
Sustainability
Technology led net zero operations, energy efficiency, GHG reduction and reporting
We think these topics might interest you
Case Studies
Trends and Insights
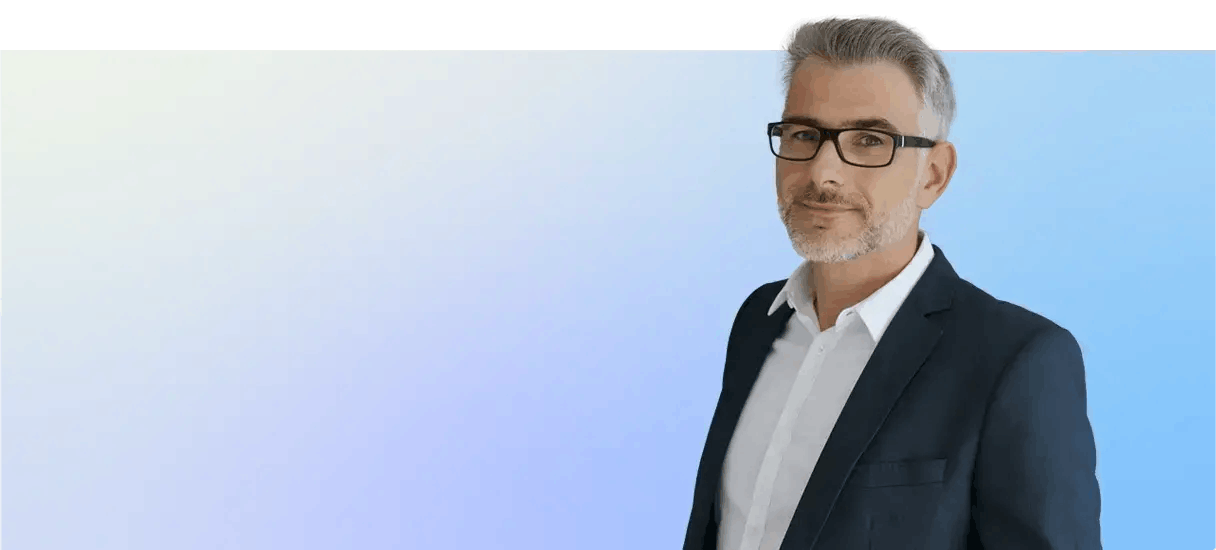
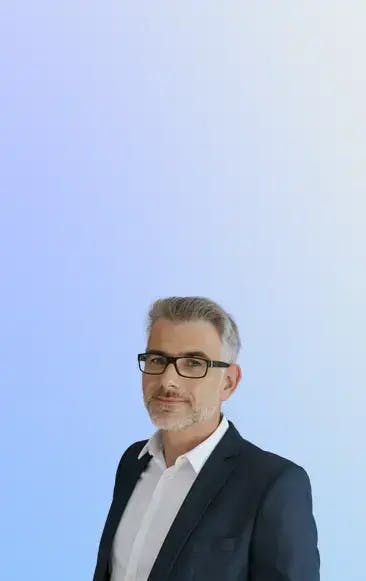
Talk to our experts
Create a resilient businesses which is scalable, adaptive and future-proof