Global mining company solves complex software integration challenge with HCLTech
The Client
The client is the second-largest iron ore company in the world. Operating in 35 countries and employing approximately 52,000 people, the client strives for environmentally responsible operations and is committed to sustainability in mining.
The Challenge
Lack of integration with third-party apps
The client had a legacy tracking system that would need to be integrated with numerous third-party logistics applications and their heavily customized SAP enterprise resource planning system.
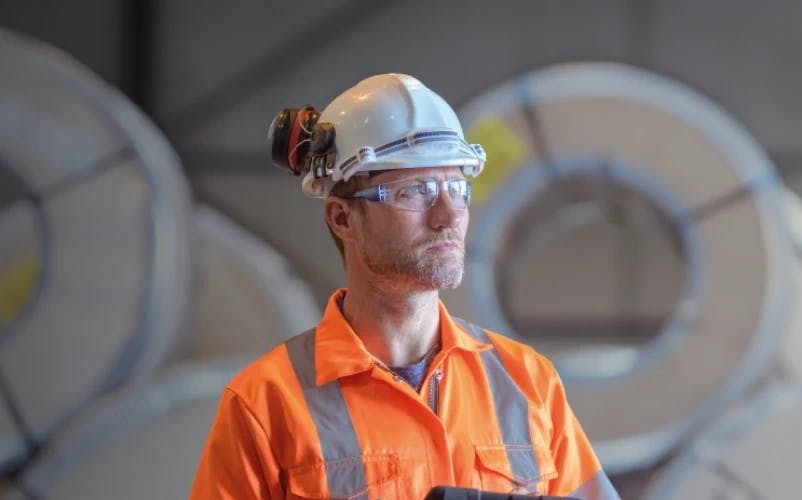
The Objective
Improve visibility into asset tracking across the organization
The client’s iron ore division needed an intelligent asset tracking system that would allow people to quickly find parts and ship them to the right locations within a set schedule.
The system also needed to give decision-makers full visibility of asset tracking data.
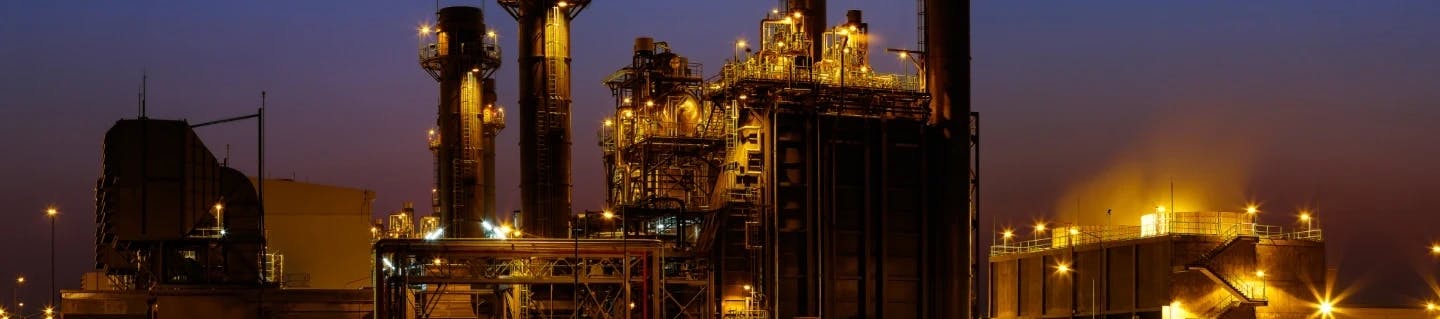
The Solution
Deliver an integrated architecture to enhance productivity and reduce costs
The client engaged HCLTech to piece together this complex integration puzzle. HCLTech architects then worked with key stakeholders to get a full understanding of the project’s complex requirements.
Challenges included:
- Migrating a significant amount of data
- Collaborating with many business and technical stakeholders across the three organizations
- Maintaining business continuity during the migration
To ensure the project did not interfere with the client’s daily operations, HCLTech deployed both local and off-shore teams to complete software development and integration activities overnight, an ideal scenario for the Perth-based project. Using this process, HCLTech integrated 20 different software applications including SAP. The manager of the Asset Management Supply Chain Iron Ore division was delighted with the result.
“Thanks, HCLTech, for your support and effort over the last two years. Track and Trace is an ambitious project with many interlaced datasets and interfaces with a highly customized ERP, changing schedules, a massive data migration and the challenges of working with many stakeholders. I appreciate your hard work, patience, adaptability and most of all persistence in helping us with a very complex project. It has been a pleasure working with such a professional team that has supported us for so long and I'm very proud of the working partnership we have built with your team.”
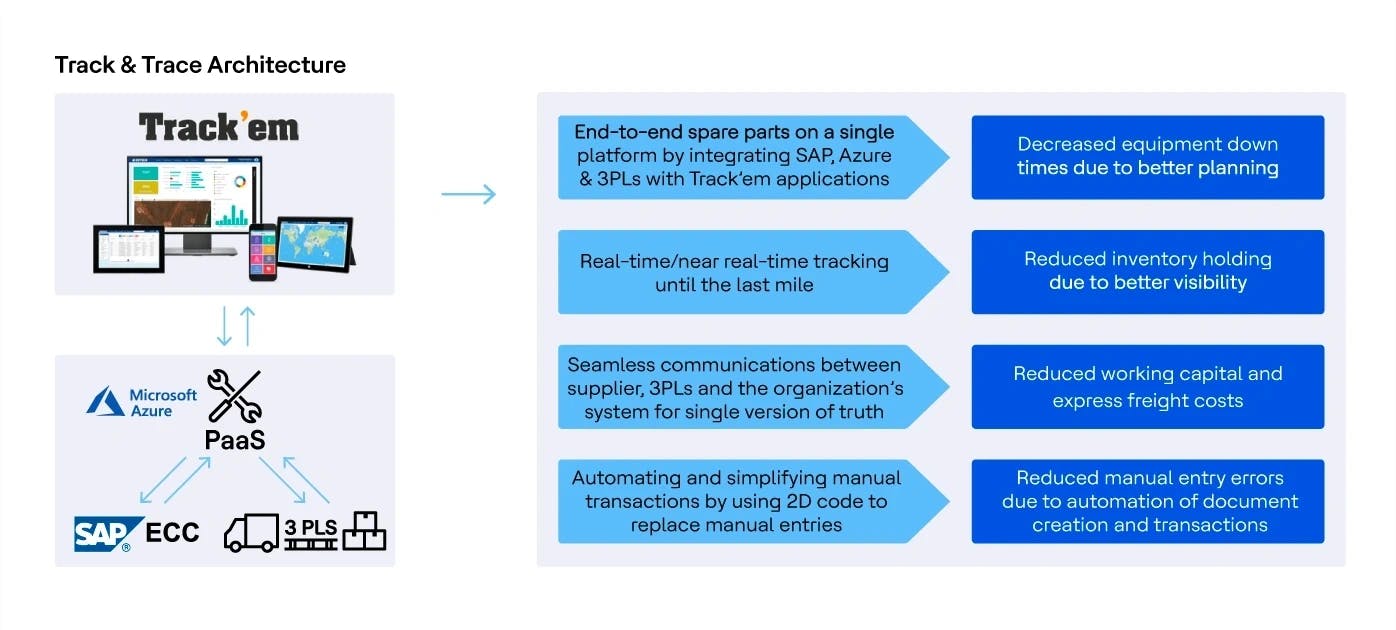
The Impact
Automating tracking processes and unlocking new insights
The client’s team now has access to a unified platform that provides end-to-end visibility of the movements of parts and equipment throughout their global organization.
The solution has been rolled out to several warehouses and the results are already promising.
- Parts can be identified in consignments and tracked to their destinations
- Processes and transactions that were previously manual and time-consuming are now either automated or simplified, improving workforce productivity and reducing errors
- Up-to-date asset-related data is flowing through to managers’ SAP dashboards, enabling them to make more informed decisions and streamline warehouse and logistics operations
By improving planning and overall efficiency, they no longer rely on costly express freight deliveries to keep to maintenance schedules. Furthermore, with powerful asset tracking and 3PL data integrated into the client’s ERP system, further efficiencies, such as reducing inventory holding costs, will be enabled.