Revolutionizing manufacturing operations for a global healthcare company
The Challenge
The company had grappled with several operational challenges in inventory management, causing disruptions in production planning and escalating operational costs. In their quest for a partner capable of delivering a transformative impact through material visibility, tracking and management, the company turned to HCLTech. They were looking for a partner to bring not only an industry-grade solution to support multiple technologies, but also end-to-end solution ownership, including tracking technology and hardware selection, installation, deployment and integration with their existing enterprise IT landscape, enabling expedited realization of business benefits.
A major issue at that time was the lack of visibility into raw material inventory, work-in-progress (WIP) sub-assembly and finished goods inventory. This gap between ERP system records and the actual onsite manufacturing plant floor led to significant production planning issues. Compounding this challenge was the utilization of manual methods for inventory audit, cycle count and reconciliation. These methods, while resource-intensive, were also prone to errors. The manual approach hindered the company's ability to maintain accurate inventory records, resulting in increased operational costs.
Furthermore, the company faced difficulties with material obsolescence due to limited adherence to First Expired First Out (FEFO) guidelines during pallet and case picking, as well as kitting processes. This lack of compliance contributed to inefficiencies in the inventory management process.
The slower inventory turn and movement were aggravated by the absence of an automated receiving and put-away process, hindering the efficient flow of materials through the manufacturing plant and impacting overall productivity. Adding to the complexities was the limited visibility into the status of receiving and consumption of raw material batches, making it challenging for the company to track and manage inventory effectively.
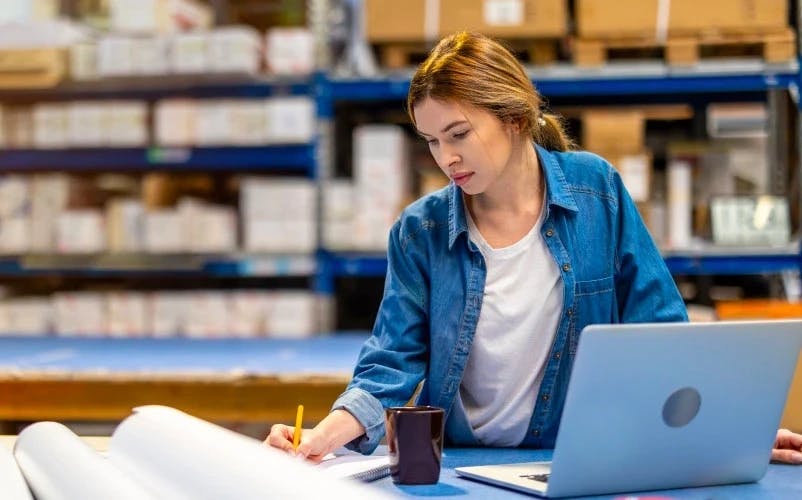
The Objective
Visibility and accuracy enhancement:
- Bringing visibility and accuracy to inventory management, with a focus on raw materials, WIP sub-assembly and finished goods.
Streamlining and automating inventory processes:
- Streamlining and automating inventory audit, cycle count and reconciliation processes to reduce manual effort and minimize errors.
Staff adherence to FEFO and FIFO guidelines:
- Ensuring staff adherence to FEFO and FIFO guidelines during pallet and case picking, enhancing overall efficiency in material handling.
Automated receiving and put-away process implementation:
- Implementing an automated receiving and put-away process to improve inventory turn and movement within the manufacturing plant.
Visibility enhancement for raw material batches:
- Enhancing visibility into the status of receiving and consumption of raw material batches for more effective tracking and management.
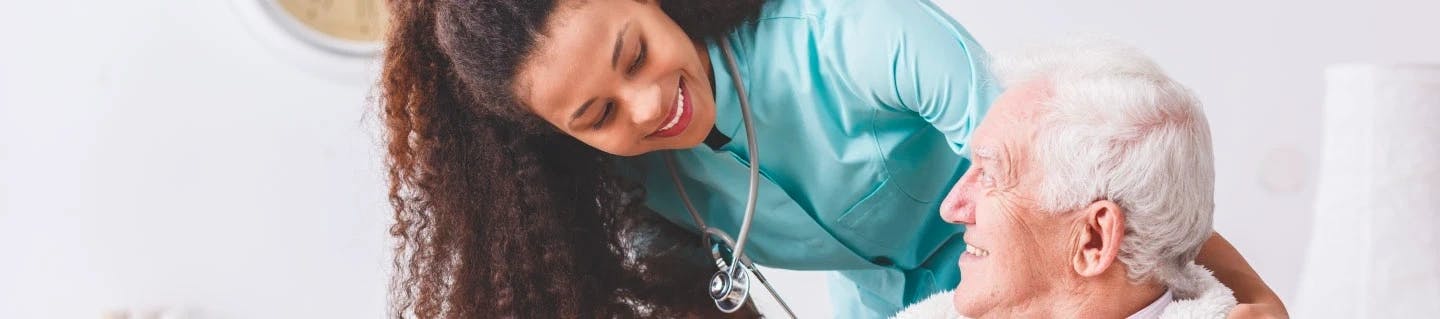
The Solution
HCLTech started this engagement with an Innovation by Design workshop along with the company’s stakeholders including their transformation, plant and IT teams. This was a joint exercise with the client to assess, identify and prioritize use cases corresponding to the company’s key business challenges and requirements in material tracking and supply chain considerations.
- HCLTech deployed Track and Trace for Manufacturing and Warehouse , powered by Intelligent Asset Tracking and Management to provide end-to-end traceability of materials in different zones across the manufacturing plant, with strategically placed sensors/readers addressing real-time locating system (RTLS) needs to track pallets,totes, closets, etc
- The solution enabled automatic monitoring and storage following FIFO and location-based inventory tracking by warehouse/rack/bin/manufacturing station.
- Customized reports and dashboards were delivered to provide real-time inventory visibility across raw material receiving warehouses, sub-assembly and filling stations, enabling decision-making to prevent stockouts and production delays.
- Automated detection of 200+ material types at entry and exit across identified zones in the manufacturing facility was introduced to enable the material lifecycle tracking of these materials from receiving to consumption.
- To ensure expedited technology adoption and realization of business benefits, new SOPs for material flow were designed and implemented. The IATM mobile app was used to provide real-time information to pickers for available placement slots, and data captured enabled reports on adherence to FEFO/FIFO business rules.
- Integration with the client’s ERP system was implemented to ensure maintaining a single source of truth.
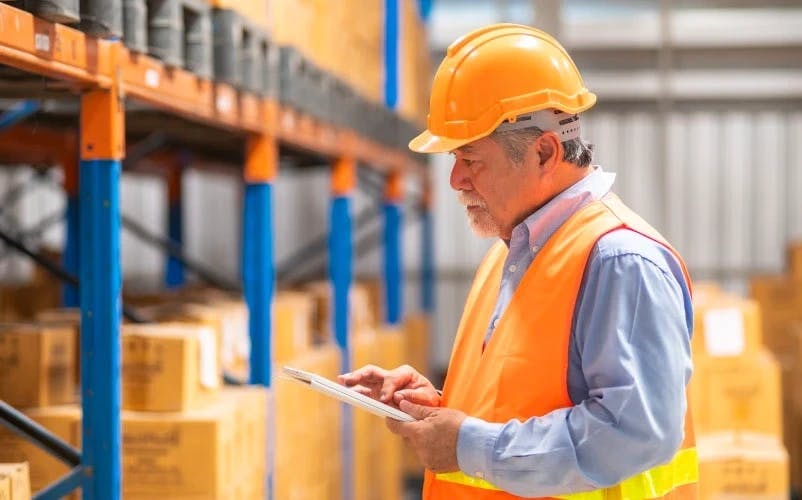
The Impact
- Real-time visibility into raw materials, work-in-progress (WIP) and finished goods inventory, coupled with automated reconciliations with the ERP system, resulted in an impressive 80-85% enhancement in inventory accuracy.
- Workflow automation led to a notable 10-20% boost in productivity, fostering operational efficiency and cost optimization by reducing labor requirements and cycle count times for both warehouse and production operations.
- The implementation of the FEFO/FIFO feature and adherence reporting reduced material wastage and obsolescence and improved overall material utilization.
- The company achieved significant improvements in inventory turnover, along with a reduction in inventory holding days and associated holding costs, showcasing the positive impact of the implemented solutions.
- Process flow optimization, facilitated by changes in material flow and streamlined operational workflows, has paved the way for successful adoption of new technologies and automation.
- Real-time visibility and transparency into raw material inventory, as provided by dashboards, empowered timely decision-making, preventing stockouts and production delays.
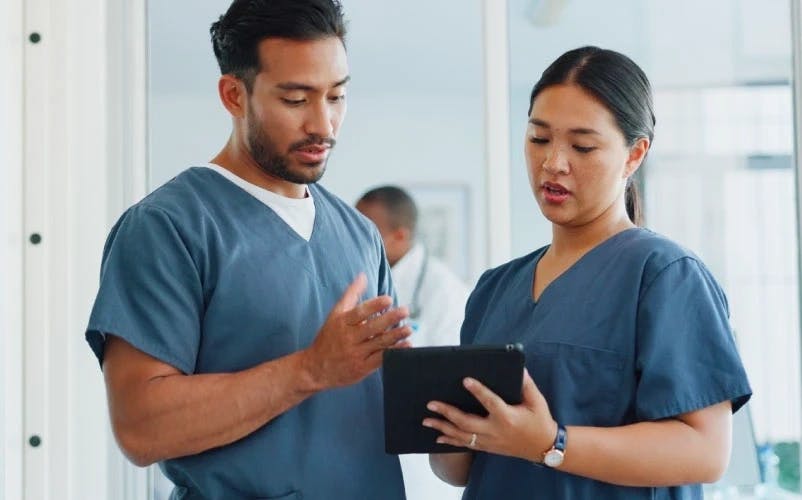