Staying Ahead of Disruption with Manufacturing Resilience
We offer an end-to-end portfolio of manufacturing operations solutions to help enterprises re-evaluate their manufacturing processes and strategies.
- Harness the full potential of the data to respond to changing customer demands and supply chain dynamics
- Enable seamless communication over the networks using protocols, from machines to shop floor devices
- Enhance productivity across production processes and supply chains through the latest cutting-edge technologies
We can help you transform the potential of your assets through real-time monitoring with improved manufacturing operations efficiency and productivity.
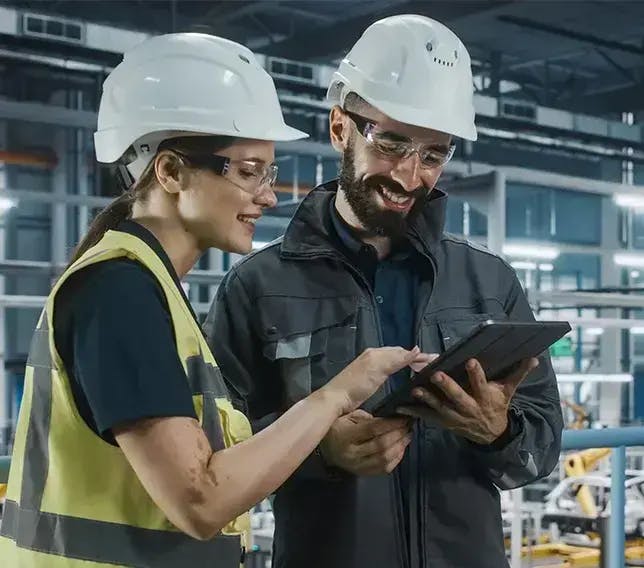
We think these topics might interest you
End-to-end Services Tailored to Unique Business Needs across Manufacturing Industries
Our customized approach ensures our manufacturing operations services and solutions cater to your unique needs.
Awards and Recognitions
HCLTech positioned as a Leader in IDC MarketScape Worldwide Manufacturing PLM Systems Integrator and BPO Services Vendor Assessment 2022
HCLTech positioned as a Leader in Everest Group’s Digital Twin Services PEAK Matrix® Assessment 2022
HCLTech is recognized as a Leader in Zinnov Zones For Engineering R&D Services 2022
HCLTech positioned as a Leader in ISG Provider Lens™ Manufacturing Industry Services – Digital Engineering – Industrial, Europe 2021
Redefining Success with Resilience, Agility and Innovation
Deeply experienced across all manufacturing industries, we offer a complete portfolio of manufacturing operations services and solutions to help enterprises enhance agility through manufacturing technology, consulting and operations, state-of-the-art labs and infrastructure, our dedicated Center of Excellence for manufacturing, digital twins and AR/VR and a strong partner ecosystem. We can help you cost-effectively overcome your biggest manufacturing operations obstacles – with sustainability at the center.
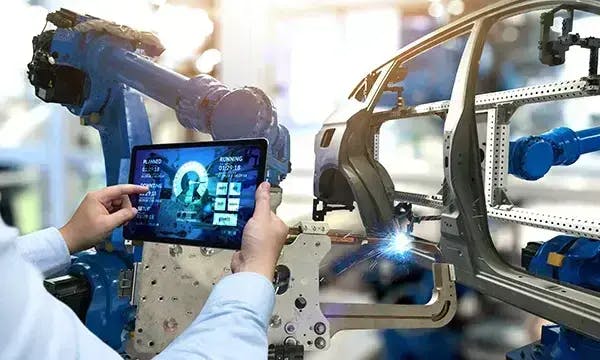
Explore Our Latest Manufacturing Operations Insights
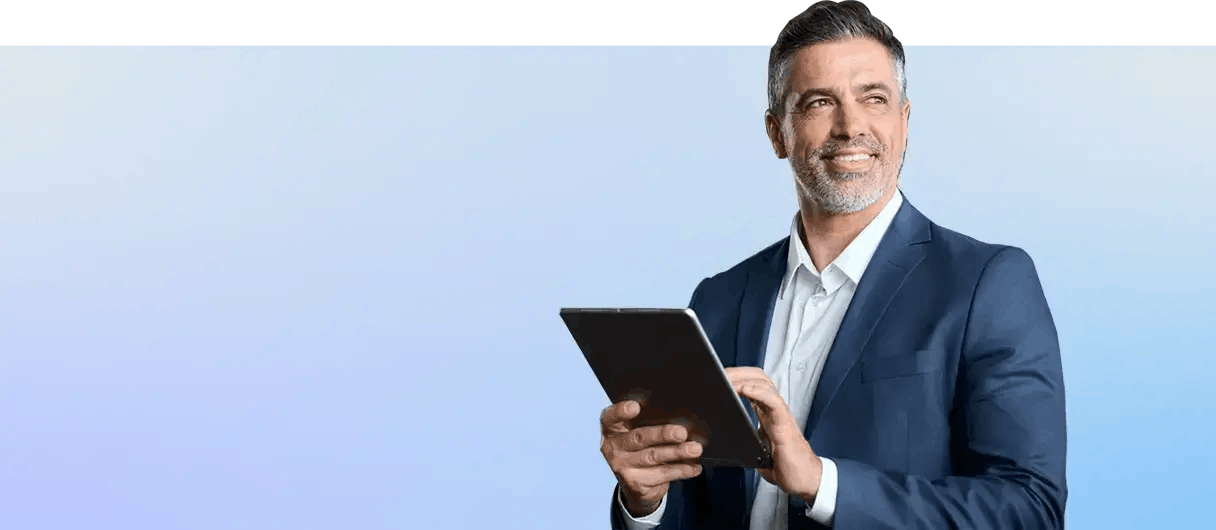
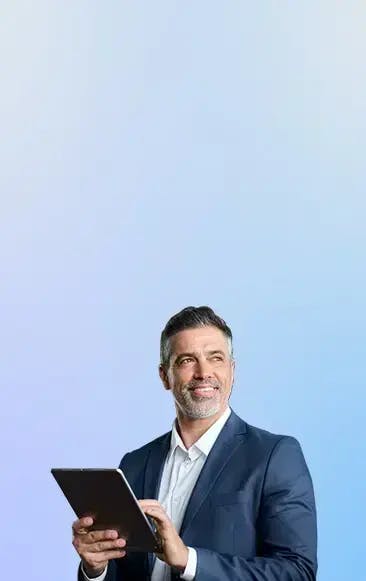
Accelerate Your Digital Plants
Connect with our manufacturing industry experts to access the vast and untapped potential of your digital plants.