Factory of the future for a leading aerospace OEM
Overview
One of the world’s leading aerospace manufacturers needed an innovative solution to reimagine their factory operations and digitally transform their legacy processes for enhanced connectivity, intelligence and integration to be future-ready.
To achieve this, HCLTech devised a digital transformation strategy that centered around a process digital twin platform. This platform helped automate the client’s production line, accelerated product development and minimized manual effort and cost.
The Challenge
Optimizing legacy processes and minimizing manual intervention in operations
The client’s legacy shop floor processes required contemporary solutions to overcome their inefficiencies. Additionally, there was a need to reduce human interventions at each level, including tasks like estimating tool usage at drilling stations during tool dispatch and manually transporting heavy tools across hangar from tool marts to working stations. These issues resulted in increased operational and labor costs, along with frequent manual errors. Furthermore, the diminished production rates that stemmed from manual processes, varying supply chain capacities and inflexible automation solutions on the shop floor extended the time to market for new products and adversely impacted business growth.
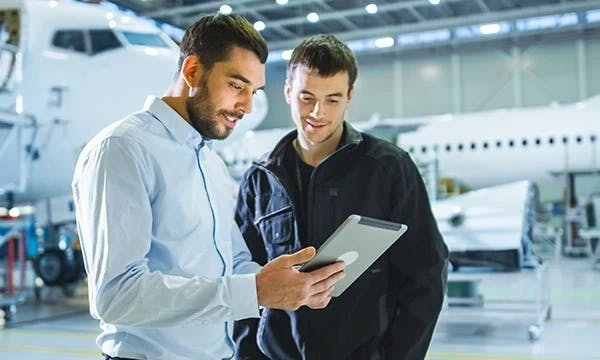
The Objective
Efficiently automate the tool dispatch process in production and implement a modernized factory
Our client actively pursued a robust solution for end-to-end automation of their current tool dispatching process in the production environment. This encompassed improving the communication between workstations and tool marts, as well as establishing real-time visibility throughout the shop floor.
Additionally, the company desired to implement automated guided vehicles (AGVs), that were controlled by a fleet management system (FMS), to handle the movement of tools throughout production lines following a manual initiation.
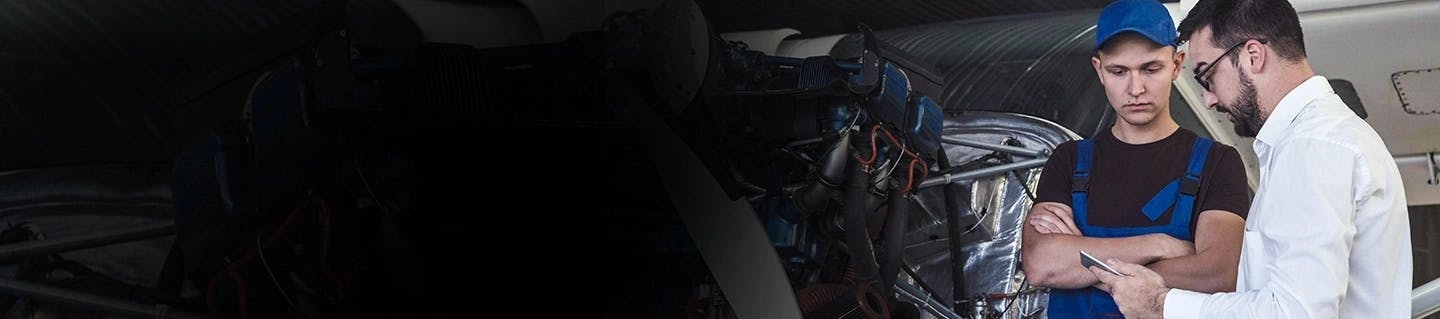
The Solution
Streamlining and automating the shop floor operations through a knowledge-based process digital twin platform
Our specialized digital engineering practice integrated multiple digital twin frameworks and solution accelerators, resulting in the creation of a process twin platform designed to track tool status, trigger orders to the tool mart for new tools and coordinate with the AGV FMS for their transportation.
The solution brought together multiple partner solutions on a semantic data platform, including PTC Thingworx IoT platform for IoT analytics and Kepware KepserverEX for edge device connectivity.
Our solution assisted in generating virtual replicas of the factory assets via aggregation and normalization of operational data captured through IoT sensors. It replicated the field behavior of the assets across the entire plant by superimposing the operational data and process conditions on digital twin models. Furthermore, predictive simulation and connected production enabled real-time visibility into the shop floor.
Our solution also utilized a robust AI/ML algorithm to navigate AGVs along pre-identified optimal paths, facilitating the completion of the next stages of the operational process.
The Impact
Accelerated production rate and significant reduction in operational costs through enhanced process efficiencies
HCLTech’s scalable process digital twin platform (for multiple plants) helped the client automate and streamline their tool dispatching process. Our best practice-based architecture and development made the process efficient and scalable for production ramp-ups. Capturing real-time plant performance information helped in tracking, monitoring and optimizing plant efficiency.
The aerospace giant saw significant business outcomes with our digital twin platform, including:
- Increased productivity (OEE) by 20% due to automation
- Reduced operational and maintenance costs by up to 30%
- Improved visibility on non-conformities, work orders and operational costs