Revolutionizing Image Processing in the Semiconductor Industry
Overview
In the ever-evolving realm of semiconductors, innovation is not just an option but a necessity for staying ahead. Our client, a world-renowned semiconductor enterprise, recognized this imperative. They identified the growing demand for a groundbreaking image co-processor to complement their application processor, ushering in a new era of enhanced device capabilities. Our innovative engineering solutions led our client to entrust us with the development of a turnkey solution.
This case study delves into the intricacies of how these challenges were navigated and conquered by the company. With a proven track record of engineering excellence, we bring innovation and reliability to the forefront of development, revolutionizing image processing for a multitude of applications. As a trusted engineering partner, we helped our client achieve success within the stipulated constraints.
Dive into this case study to learn more about this transformative journey as we partner with our client to shape the future of image processing.
The challenges
Our client, a multinational technology company, has been developing a pixel range of mobile devices where the camera/image is a critical component. They recently observed that a lot of processing associated with the captured images on mobile cameras relies heavily on the software, which not only decelerates but also degrades user performance as it consumes the valuable bandwidth of the processor. Hence, the company wanted a hardware solution to this. They partnered with our client to create a co-processor to mobile application processor, specifically designed for image processing.
Our client sought a cutting-edge solution to address the above challenges. However, achieving this required overcoming various obstacles, primarily stemming from the pressing demands of faster-time-to-market and stringent budget constraints, which mandated a remarkably tight schedule of just eight months for the development.
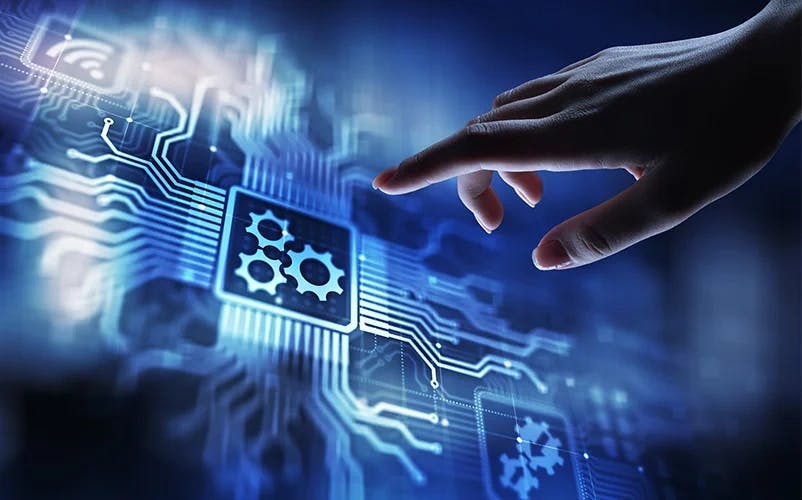
HCLTech’s approach and solution
With a restricted timeline of 32 weeks, the customer wanted a steep ramp-up in all the VLSI disciplines. As their strategic engineering partner, we came up with an innovative solution to facilitate the entire program to run seamlessly, effectively bridging the gap between vision and reality.
We provided the necessary ramp-up and brought inter-disciplinary teams together to form a comprehensive silicon design team. , managing almost 90% of the project scope. Our unique methodologies resulted in a cost saving of close to 15% and a time saving of 20-25%.
Our solutions demonstrated our prowess in assembling a top-notch team, optimizing project management, harnessing innovative verification methods, and exhibiting thought leadership in emulation and prototyping strategies among many other initiatives.
Key highlights:
- We meticulously curated a team of proficient functional managers, each overseeing critical activities such as System-on-Chip (SoC) integration, emulation, pre-silicon verification, Design for Testability (DFT), physical design, and post-silicon validation.
- Despite a tight schedule of less than 32 weeks, our comprehensive Total Functional Management (TFM) approach helped accelerate the current program and set the groundwork for its applicability to future projects.
- Our commitment to innovation can be seen through our revolutionary verification framework – the Verifast™ framework for testbenches. Coupled with Jasper Formal Verification, this addressed complex challenges, including the modeling of metastability for non-deterministic delays mirroring real hardware intricacies.
- We showcased our scripting expertise, particularly in porting Register Abstraction Layer (RAL) models. Our pioneering approach to emulation and prototyping strategy sets the bar for high-confidence hardware-software co-validation, as exemplified by the successful porting of the cutting-edge A53 processor into HAPS hardware.
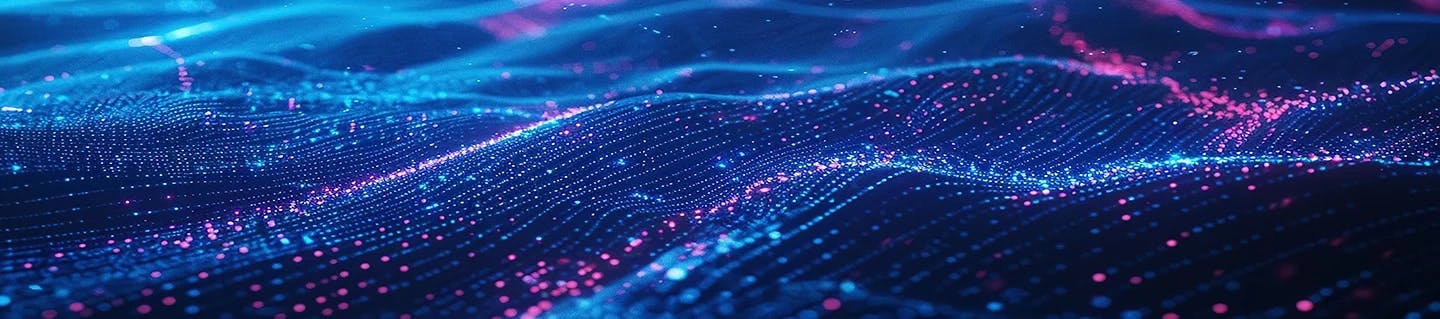
Benefits Delivered
Project Timeline Achievements:
- The project started to tape out in a record time of 32 weeks.
- The 1st spin of the silicon went into production in 15 months, which is a record for a brand-new chip.
- In addition to this, we did a lot of innovation on the power savings front and published a paper in the Design Automation Conference (DAC) as an outcome of this work. The chip went into the pixel 2 range of mobile.
Streamlined Production Process
- The initial tape-out also successfully paved the way for seamless volume production.
- Through an accelerated setup process for our new System-on-Chip (SoC), we managed to slash the verification cycle time by an impressive eight weeks. This not only fast-tracked our development timeline but also augmented our confidence levels by a significant 20% through rigorous formal verification.
Efficiency and Rapid Bug Fixing
- Our commitment to efficiency is evident through our swift turnaround time for bug fixes boasting a median of just one day. This rapid response ensured the timely delivery of the project leaving no room for delays.
- Moreover, we achieved a notable reduction in RTL (Register-Transfer Level) bugs, bolstering our design confidence to new heights.
As a trusted engineering partner, we facilitated our client to achieve success within the stipulated constraints, revolutionizing image processing for a multitude of applications.