Delivering actionable intelligence to the last tactical mile
As the workplaces have been witnessing upgradation through technology disruptions, and digital transformation, there is a clear need for re-skilling, upskilling, and cross-skilling of industrial workforces to help them prepare for the future of work. The industrial workforce has been confronted with an impending digital skill gap that can impede the best workplace technologies from realizing the business benefits, whether it is task-based insights, equipment assessment, or performance evaluation.
A digital workplace transformation for the industries cannot be complete without augmenting the digital dexterity of the industrial workforce.
Our Smart Industrial Assistant (SIA) is transforming the future of work for the frontline industrial workforce by delivering actionable intelligence to the last tactical mile. This empowers technicians to have conversations with machines on error codes, maintenance procedures, service bulletins, and past performance.
Data extraction and insight generation
By applying innovative Machine Learning (ML) and Natural Language Processing (NLP) techniques to the centralized and edge data streams, the SIA provides real-time, context-driven guidance, and insights to end-user mobile/wearable devices/Microsoft Teams/any enterprise system.
The automated pipeline extracts structured and unstructured technical and domain data from industrial datastores.
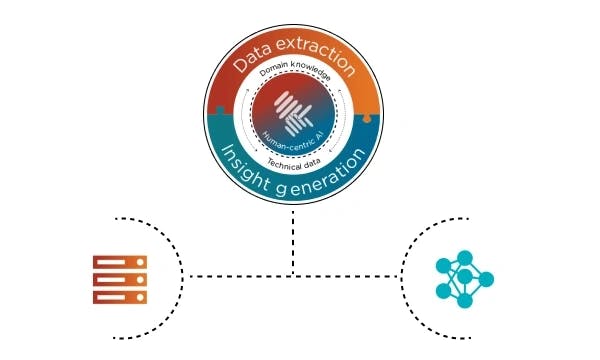
We think these topics might interest you
Centralized data
The automated pipeline extracts structured and unstructured technical and domain data from industrial datastores.
- Enterprise systems data
- Enriched data & analytics
- Service and support data
Edge data
Live data from IoT and edge-based devices are integrated into our dataflow framework
- Connected Sensor Feeds
- Field Service Data
- Discrete User Data
Better decisions about the last tactical mile
Last-mile analytics
This solution enables enterprises to extract, fuse, and correlate structured and unstructured enterprise data. Most large industrial data environments contain a wide variety of disparate and disconnected data sources, including non-standard data sources that have hand-written notes, scanned PDFs, service bulletins, operation manuals, peer notes, and live equipment sensor data feeds.
The unique application techniques (ML and NLP) of SIA insight engine derives actionable intelligence from enterprise datastores.
AI-enabled work instructions
An advanced virtual assistant that delivers AI-enabled work orders, task guidance, digital work packages, system and equipment notifications, proactive recommendations, safety alerts, warnings in real-time and contextual insights to industrial workers in real time. It understands a user’s location and role, as well as equipment status, to define and deliver intelligent guidance through an intuitive conversational interface on a mobile, wearable device or Microsoft Teams. It is uniquely designed for the on-the-job requirements of technical personnel operating, repairing, and maintaining complex equipment.
Benefits
New operational insights
Increase employee productivity and equipment uptime through enterprise intelligence on the front lines
Enhanced decision-making
Real-time intelligence on the last tactical mile increases productivity and empowers ‘first-time right’ performance
Human-centric digital tools
Increase employee engagement while decreasing technical support escalations
Skilled workforce development
On-the-job upskilling, accelerating time to proficiency, and improving digital literacy