
Overcoming OT backup challenges in Industry 4.0
Organizations across various sectors face a series of formidable challenges when it comes to ensuring the resilience and continuity of their OT environments.

Reactive programming in Java
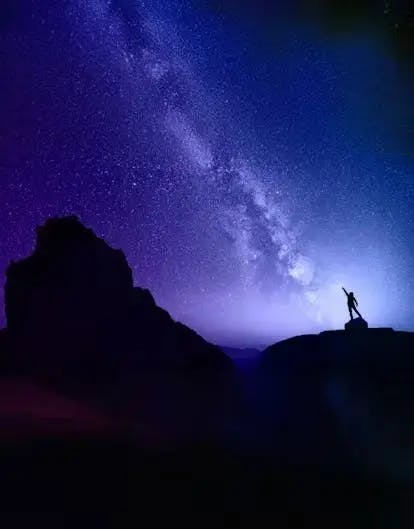
HyRISE: Enabling future-ready SAP transformation
Discover how HyRISE empowers SAP transformation through seamless S/4HANA migration, driving efficiency and innovation.

How AI is reshaping healthcare
AI is powering the development of innovative medical devices and technologies that have the potential to revolutionize healthcare delivery.
All Blogs

Digital synergy in M&A: Aligning cloud, security and workplaces for success
Explore how cloud, security and digital workplace integration drive M&A success, ensuring agility, security and value realization from day one.

Bridging the lexicon gap and teaching GenAI to speak enterprise
The blog aims to address the "lexicon gap" in GenAI by advocating for semantic layers to enable accurate, scalable and trustworthy AI-driven insights in structured enterprise data environments

The impact of AI and GenAI in quality management automation
Explore how GenAI is driving intelligent automation in quality systems, ensuring improved compliance and enhanced operational performance in the life sciences industry.

An in-depth exploration of AI in casino operations
This blog explores the cutting-edge panorama of technological advancements and the intricate architectural considerations that illustrate how AI is revolutionizing casino operations.

Why AI-driven DevSecOps is reshaping software engineering?
Reshaping how software is planned, built, secured and delivered

How AI and ML enhance OT threat detection and intelligence
The modern OT ecosystem operates at a high velocity, leaving little room for reactive threat responses. AI and ML enable predictive threat intelligence by utilizing pattern recognition.

ARGiS revolutionizes industrial asset management by integrating IoT data, ML predictions and a multilingual chatbot for improved maintenance and performance.

Building blocks for a NextGen AI-powered IT audit program
Now is the time to leverage the future of AI-driven auditing and minimize risks while maximizing your organization’s agility in an ever-changing digital world.

This article explores how HCLTech and NVIDIA are driving Physical AI to transform enterprise OT with real-time intelligence, autonomy and scalable AI-powered industrial solutions.

HCLTech and AWS are transforming product design by addressing legacy system challenges, enhancing collaboration, agility and innovation, while ensuring security and compliance in a digital landscape.

Overcoming GenAI adoption fears: A phased approach to business value
Addressing GenAI implementation challenges through systematic, risk-mitigated adoption.

AI/GenAI in data centers: Trends, use cases and recommendations
AI and GenAI, including small language models, are transforming data centers by enhancing efficiency while addressing complex problems and highlighting strategic recommendations for adoption.
Our Areas of Expertise
With expertise in Digital, Engineering and Cloud, we deliver solutions that fulfill the traditional, transformational and future needs of clients across the globe.
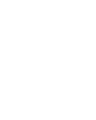
Digital
HCLTech’s end-to-end Digital offerings enable enterprises to increase business resilience, improve operational efficiency and deepen client engagement.
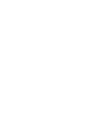
Engineering
HCLTech Engineering and R&D services (ERS) empower enterprises to improve time-to-profit, accelerate product development and maximize return on innovation.
Explore our Engineering Services
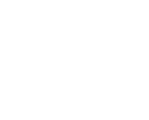
Cloud
HCLTech’s exclusive CloudSMART offerings and services enable organizations to optimize cloud to accelerate innovation and agility at scale.
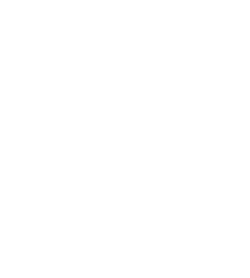
AI
HCLTech empowers organizations across industries to identify and seize opportunities to leverage AI and GenAI to automate and accelerate business processes.