Video
Section CTA
Agentic AI: The next phase of enterprise transformation
Piyush Saxena on moving beyond AI pilots and proofs of concept
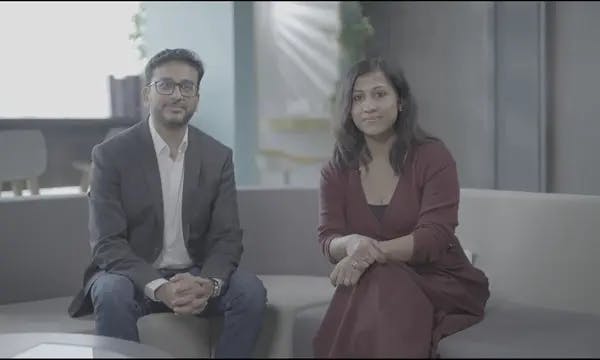
Piyush Saxena on moving beyond AI pilots and proofs of concept
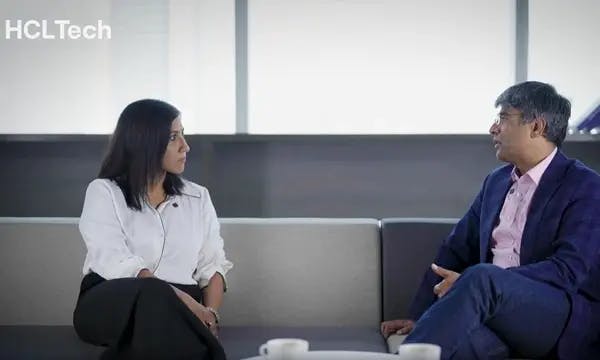
Playing now
Total Experience: A necessary strategy or just another buzzword?
Gaurav Bhatia, CMO of PenFed Credit Union, speaks with Mousume Roy, highlighting the role of Total Experience in enhancing organizational resilience
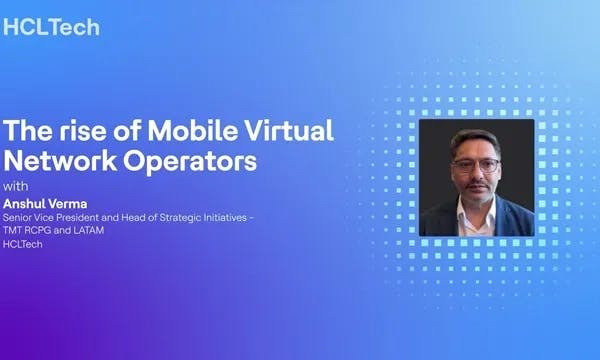
Anshul Verma, SVP and Head of Strategic Initiatives at HCLTech, reveals how Mobile Virtual Network Operators will reshape telecom markets worldwide, with Brazil as a key player
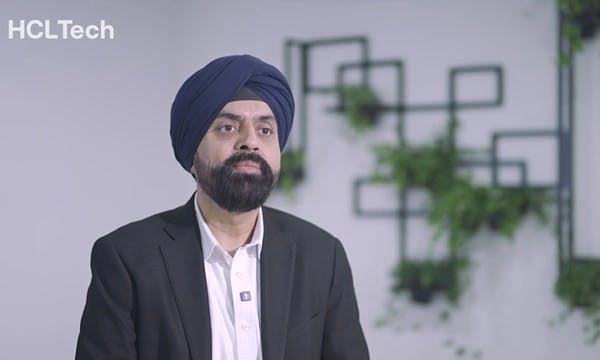
Playing now
Strengthening the digital spine: How telcos can thrive through network transformation
Gurpreet Singh Kohli, SVP, Telco & Enterprise Networks at HCLTech, discusses how telcos can drive growth by modernizing their digital spine with agile tech, innovation and strategic partnerships
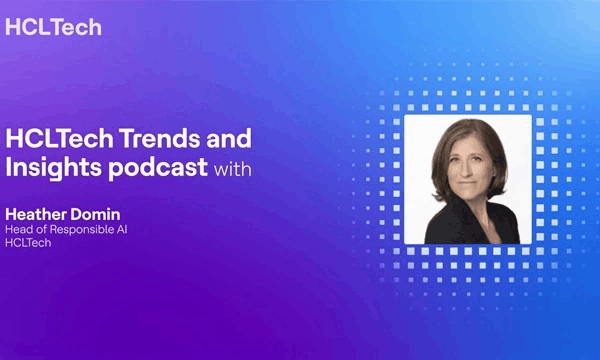
Heather Domin, Head of Responsible AI at HCLTech, joins Nick Ismail on the HCLTech Trends and Insights podcast to discuss why Responsible AI is now viewed as a competitive advantage and how organizations can best implement more ethical standards
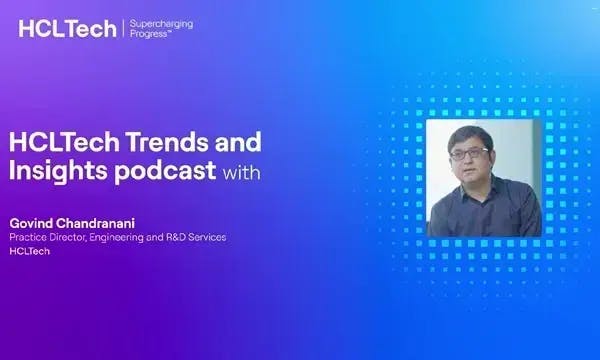
Govind Chandranani, Practice Head of Engineering and R&D Services at HCLTech, discusses how enterprises adopting GenAI must embed responsible governance to balance innovation with trust and compliance
Podcast
Section CTA

0:00
progress
00:00
Subscribe to the HCLTech Newsletter
for our latest news and insights