Is Your Business Ready for the Future?
Rising customer expectations and evolving behavior. Personalized buying options and the rise of private labels.
The consumer packaged goods (CPG) industry stands at the brink of a digital revolution.
The expansion of disruptive technologies – like artificial intelligence (AI), machine learning (ML), internet of things (IoT) and data analytics-driven offerings – creates a variety of new opportunities and challenges.
At HCLTech, we're in the business of helping our CPG customers identify and seize those opportunities to attain a competitive advantage.
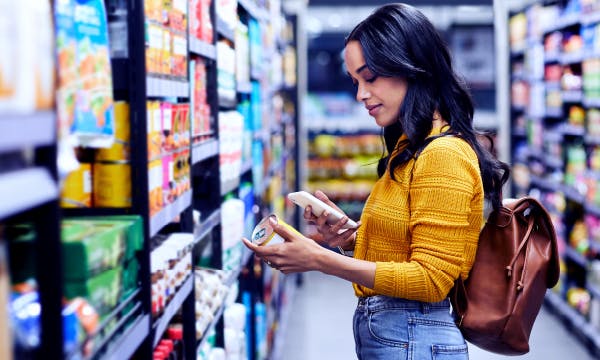
Discover Enterprise Solutions for the CPG Industry
Our solutions combine data-driven insights with digital technology that leverages the convergence of people, data and technology such as AI to help CPG organizations innovate beyond the product.
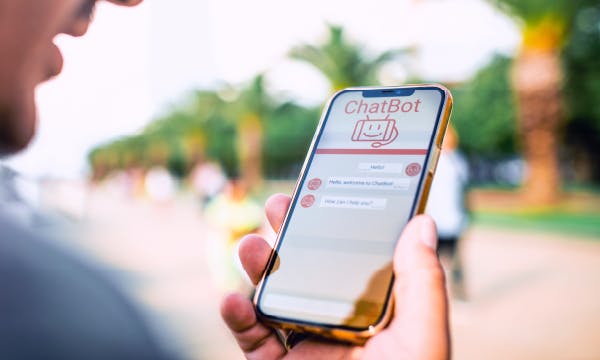
Elevate your customer engagement
Revitalize your customer journey by providing seamless, captivating and personalized experiences through powerful digital engagement.
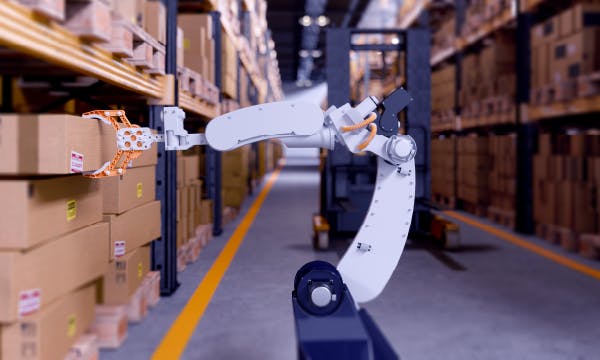
Streamline your trade effectiveness
Achieve optimal trade effectiveness through improved on-floor availability, shelf space management and planogram compliance using best-in-class AI and ML technologies.
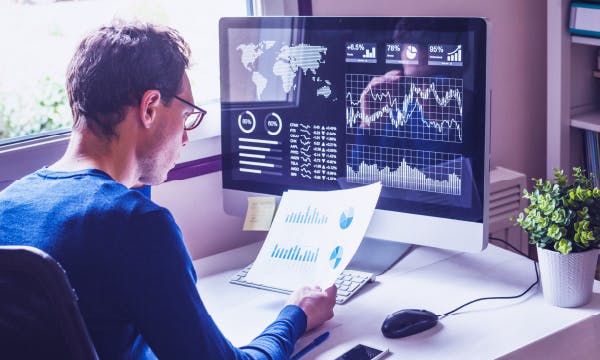
Enhance your pricing and revenue management
Harness the power of customer preferences, demand fluctuations and market insights to establish optimal pricing strategies for your products.
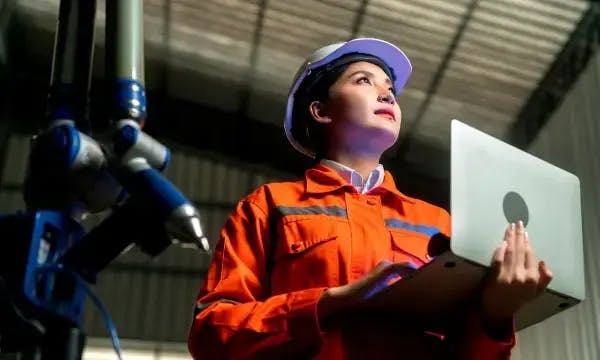
Revolutionize your manufacturing with intelligent technology
Revamp your manufacturing process through interconnectivity and advanced data analytics to unlock unparalleled resilience, agility and preemptive tracking of machines, parts and materials.
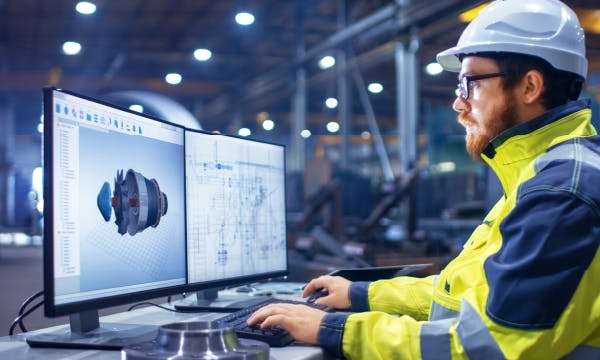
Drive innovation with advanced product design and PLM
Revolutionize your product design-to-manufacture process by leveraging the cutting-edge technologies of real-time data IoT, digital twins and advanced analytics.
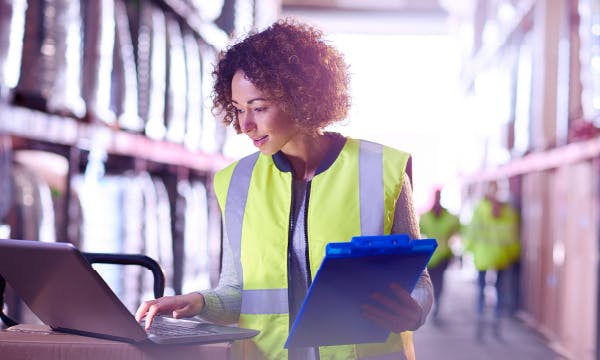
Elevate your supply chain planning and execution
Streamline your supply chain processes and achieve unparalleled results with our advanced methodologies.
We think these topics might interest you
Transforming CPG Companies
for Over 2 Decades
Consumer goods companies get the best outcomes when they work with a technology partner to help them accelerate their journeys toward modern, data-driven and digitally connected agile enterprises.
Based on decades of experience in working with global CPG brands, our deep software engineering heritage and significant investments in emerging technologies, HCLTech is the right technology partner to help CPG enterprises move to CPG 4.0.
Food companies are our clients
Beverage companies are our clients
Consumer and personal care companies are our clients
Experience in retail and CPG
Success Stories Highlighting Our Impact on Our CPG Clients
Discover more about how HCLTech has helped consumer goods clients just like you.
Explore Our Latest Insights into Consumer Products Solutions
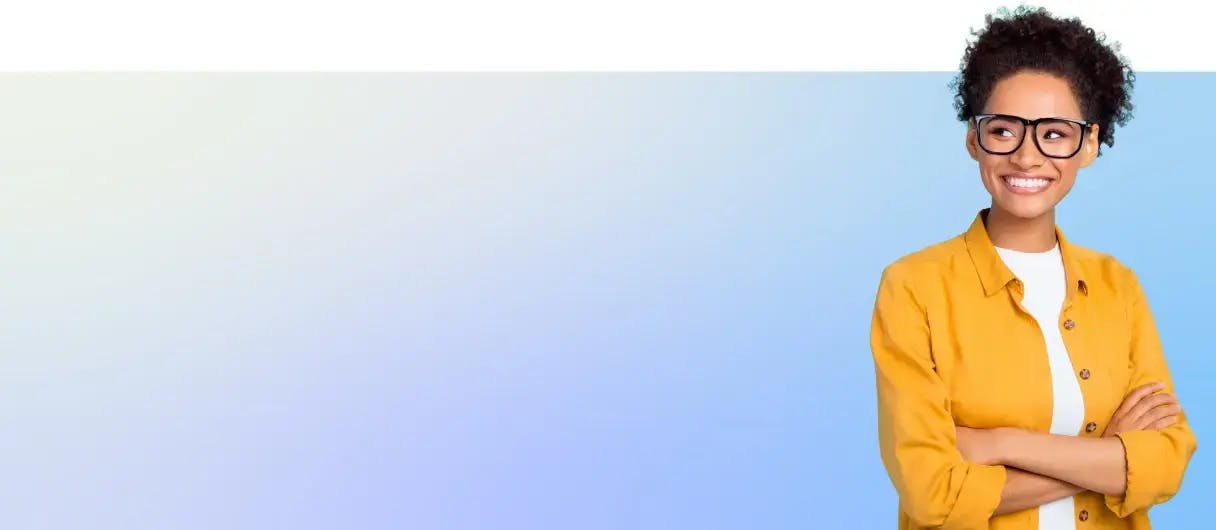
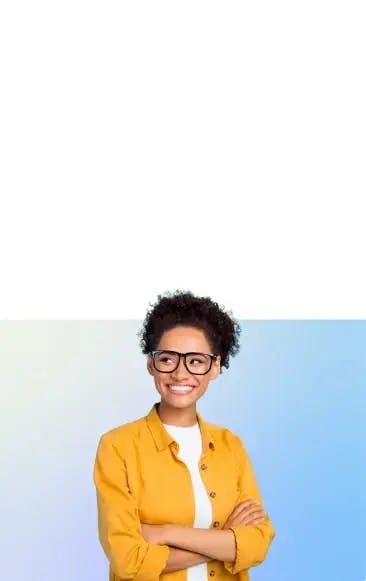
Move Fast. Move Better.
Partner with HCLTech.
Take your enterprise to the next level with our CPG industry solutions.
Subscribe to the HCLTech Newsletter
for our latest news and insights